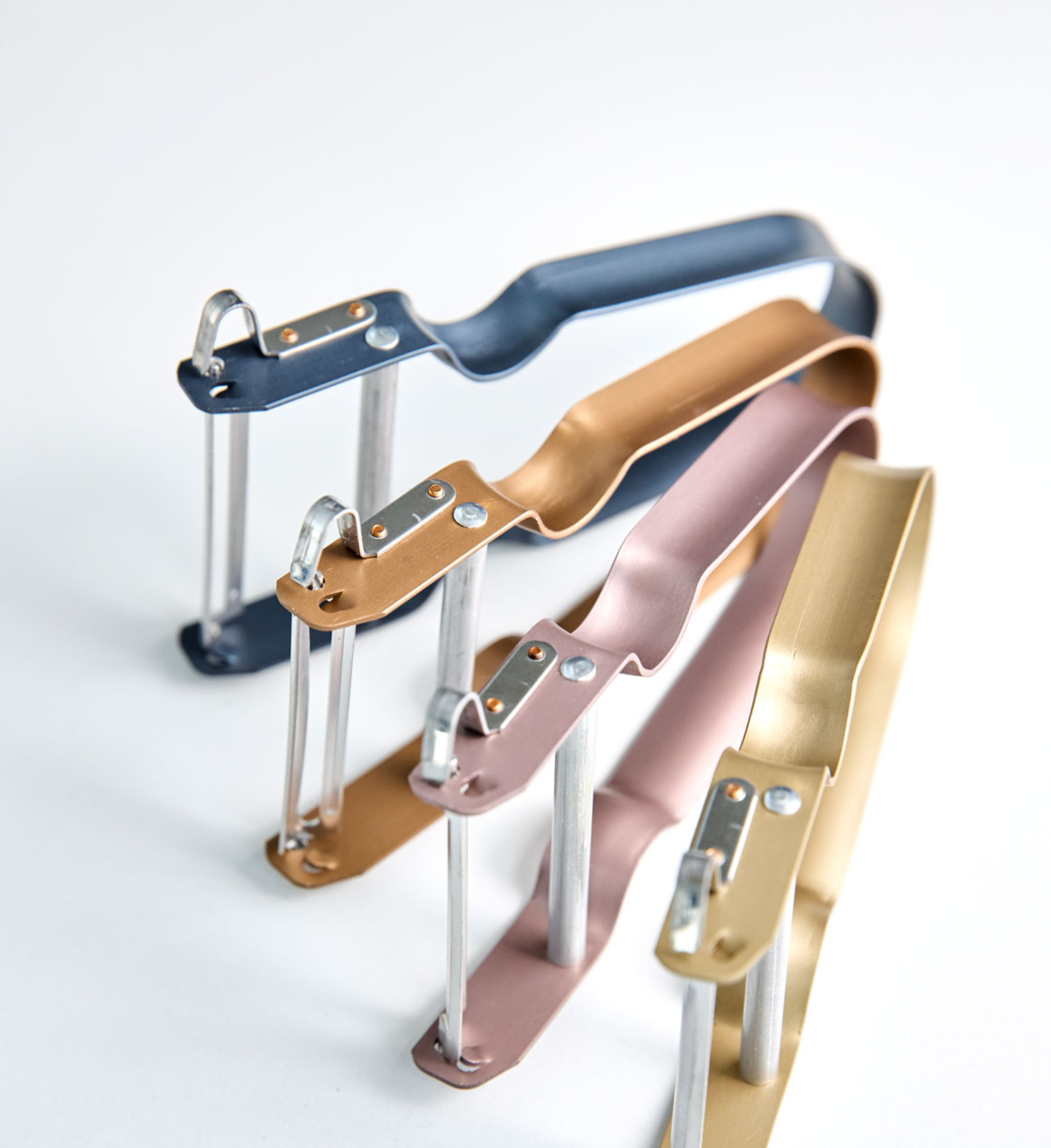
Depuis 1947, le plus célèbre des éplucheurs en aluminium n'a pratiquement pas changé de design. Il est aujourd'hui fabriqué, avec passablement de travail manuel, à Delémont.
Vite! Il reste trois jours pour emballer le lot d’éplucheurs prévus en boutiques pour le mois suivant. Et voilà sept personnes à table qui déplient chaque boîte livrée par l’imprimerie et y glissent l’éplucheur correspondant… Il y en a des milliers: courage! C’est que la production du plus célèbre des éplucheurs, le Rex, est en cours de transformation. La machine à emballer va arriver début 2022, en attendant on se débrouille comme on peut.
Dans une vie précédente, jusqu’à l’automne 2020, quand l’entreprise Zena fabriquait encore le petit outil, dont il a fait la renommée durant trois générations, cette étape de l’emballage se confiait à des ateliers protégés. Mais voilà que Victorinox rachète Rex – et toute la belle histoire qu’il incarne. Il sera l’un des joyaux – à côté, évidemment, des célèbres couteaux suisses. «Avec cet investissement, nous pouvons enrichir notre division stratégique «couteaux de ménage» avec des produits intéressants et continuer à aller de l’avant avec courage et esprit d’entreprise, même en ces temps inhabituels», déclare Carl Elsener, CEO de Victorinox.
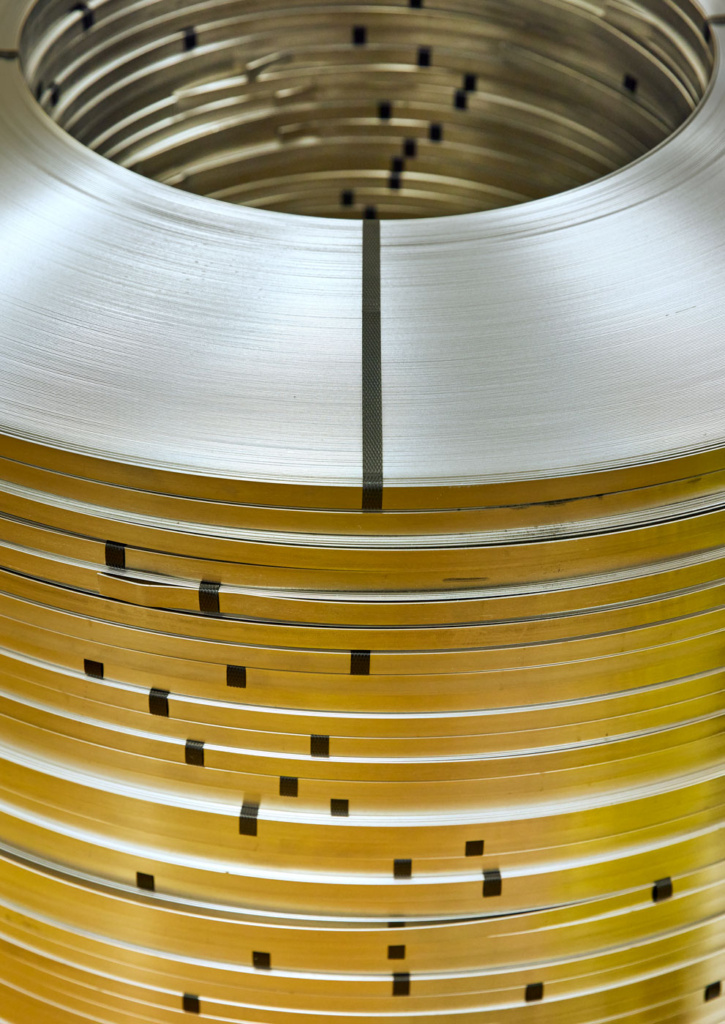
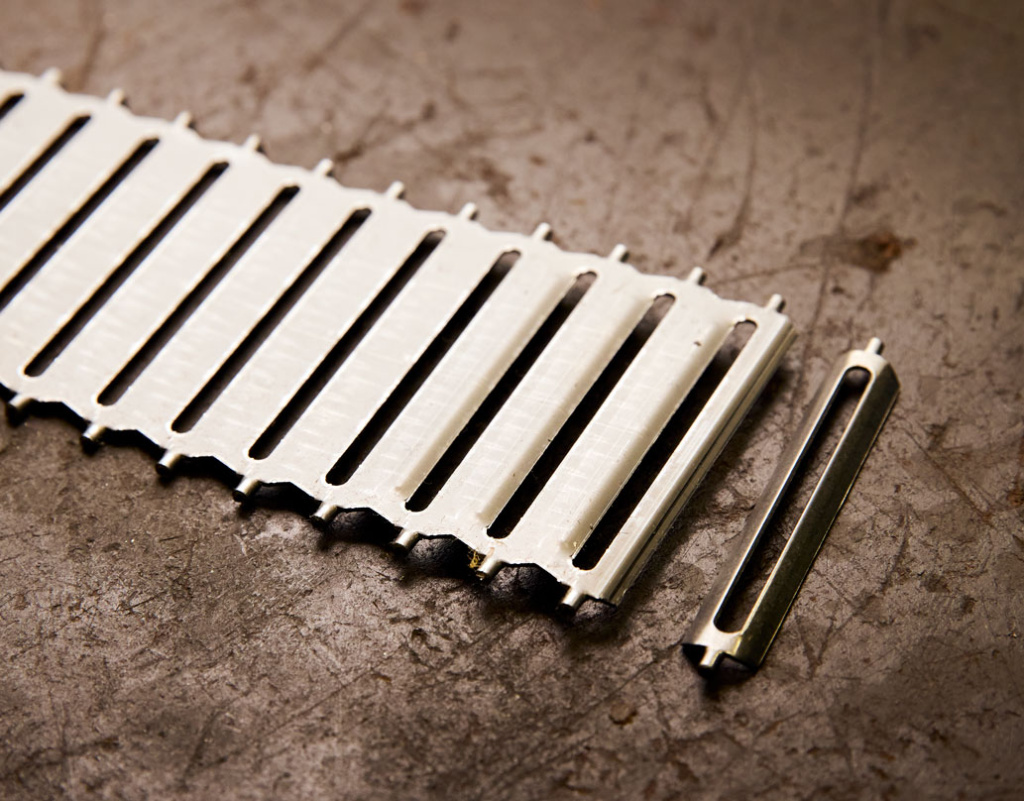
Flashback. La légende veut qu’Alfred Neweczerzal, marchand forain et bricoleur, ait souvent été de corvée patates durant son service militaire. Il aurait alors imaginé un outil qui lui permette d’accélérer la tâche. Petit, aiguisé, simple de concept, léger en main (20 grammes!): voilà notre Rex. L’inventeur a déjà une entreprise à son nom, où il fabrique des râpes et autres ustensiles de cuisine. En 1947, il dépose un brevet pour son nouveau favori et le numéro de patente 11002 restera gravé sur le manche jusqu’à l’actuel mois d’octobre, quand le logo Victorinox le remplace.
Souvent primé pour son design intemporel et son ergonomie, il a même eu l’honneur d’un timbre-poste. Une boucle d’acier acéré lui permet d’enlever les yeux des pommes de terre et deux cousins agrandissent bientôt la famille: les modèles Star en acier (disponibles avec des lames dentées) et Rapid (avec manche en plastique). Mais le vrai de vrai reste Rex. Et tant pis si l’aluminium s’oxyde au lave-vaisselle.
400 pièces à l’heure
C’est donc ce monument miniature qu’a acquis Victorinox. La production a migré à Delémont, en janvier, à la suite de la fermeture de l’usine d’Affoltern qui l’a vu grandir. Le voilà sur le site racheté en 2005 au coutelier Wenger. Une dizaine d’employés, sur la centaine qui travaille à la production (couteaux et montres), veille à ce que le petit dernier soit traité en roi. Tout commence par un rouleau de ruban d’aluminium. Le dérouleur le transporte sur une machine à découper, qui perce les trous de maintien de la lame et de la butée, qui modèle les deux creux et frappe le logo. «Le processus a l’air simple, explique Laurent Weber, responsable de production. Mais il faut tout de même veiller à ce que l’entre-axe soit placé juste, que le marquage soit propre.» La machine travaille avec son coéquipier humain.
Si le modèle est prévu en couleur, c’est à cette étape que les pièces en aluminium partent à St-Gall, pour un bain de pigments. «C’est l’avantage de l’aluminium, précise Laurent Weber, il est facile à anodiser.» Outre la classique version nue, Rex existe en rouge suisse et dans une prestigieuse édition festive or 24 carats. Et l’an prochain – chut, c’est encore un secret – verra des collections capsules aux nuances contemporaines. Le premier quatuor? Blueberry, lavande, cannelle et cajou…
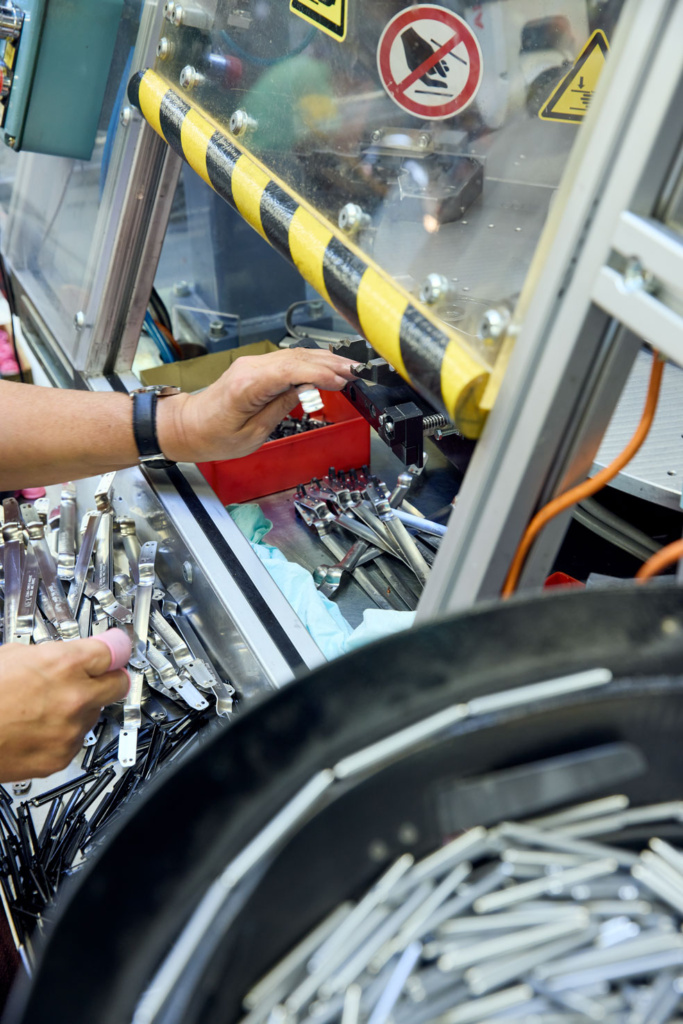
Une seule machine assemble les quatre pièces qui constituent Rex.
Pendant que la poignée prend son bain coloré (ou pas) se fabrique la lame d’acier. Une presse la découpe en 10 étapes, toujours plus finement, puis l’incurve légèrement. Passage ensuite à l’aiguisage: le chargement se fait à la main sur la vieille machine héritée de Zena (la nouvelle arrive!). Ensuite, le robot pousse la lame vers la meule, qui en aiguise la surface, d’un côté, de l’autre, dans un grand flot d’eau émulsionnée, pour éviter que la pièce ne chauffe trop et n’y perde en solidité. La lame acérée tombe au final dans un bain d’eau, pour amortir la chute et préserver le coupant.
Ne reste alors plus qu’à assembler, dans un processus semi-automatique. La lamelle d’aluminium se charge manuellement, puis la machine fait tourner la pièce sur plusieurs étages. Elle lui rive le coupe-œil en acier, assemble l’axe d’aluminium, plie l’outil, le rive et finalement insère la lame dans ses orifices. Chaque heure, 400 pièces tombent ainsi dans le bac. Victorinox espère en produire quelque deux millions par an en rythme de croisière. Après? Ne reste qu’à croiser les doigts pour que la machine à emballer ne prenne pas de retard…
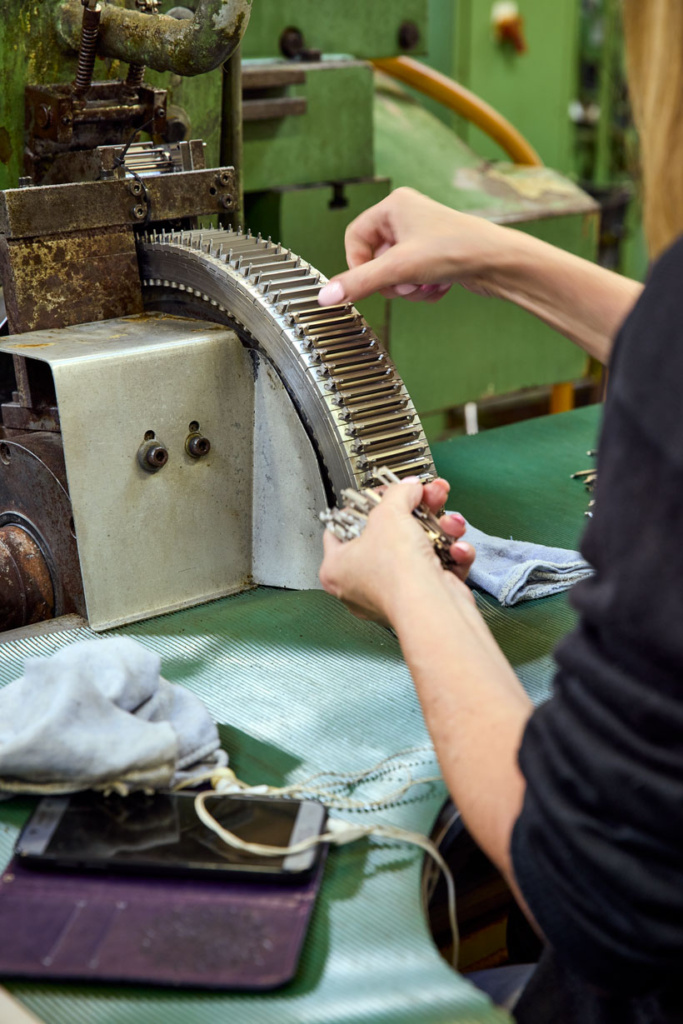
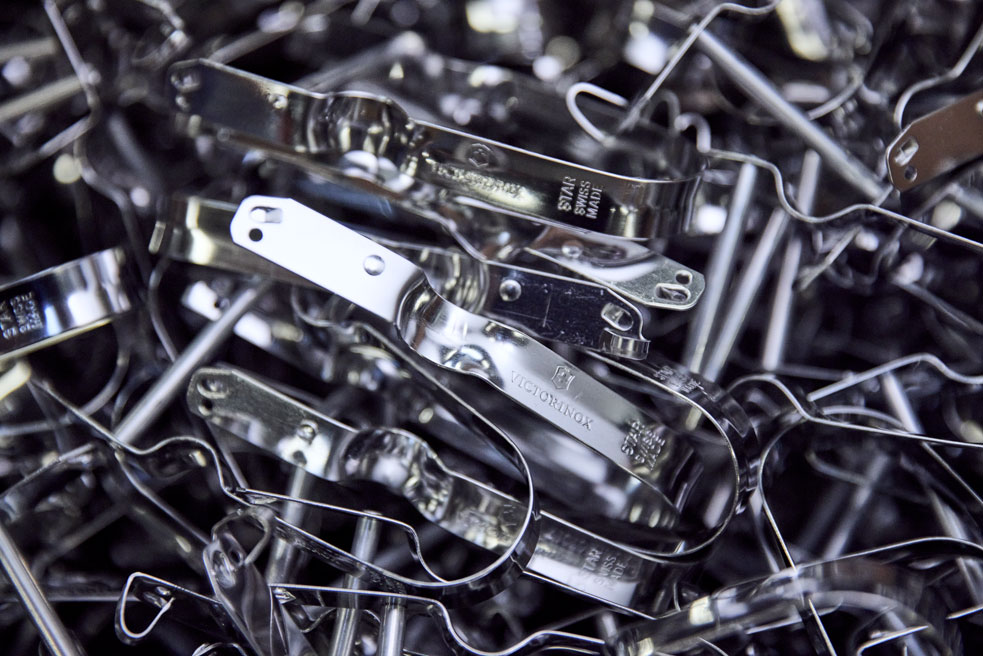
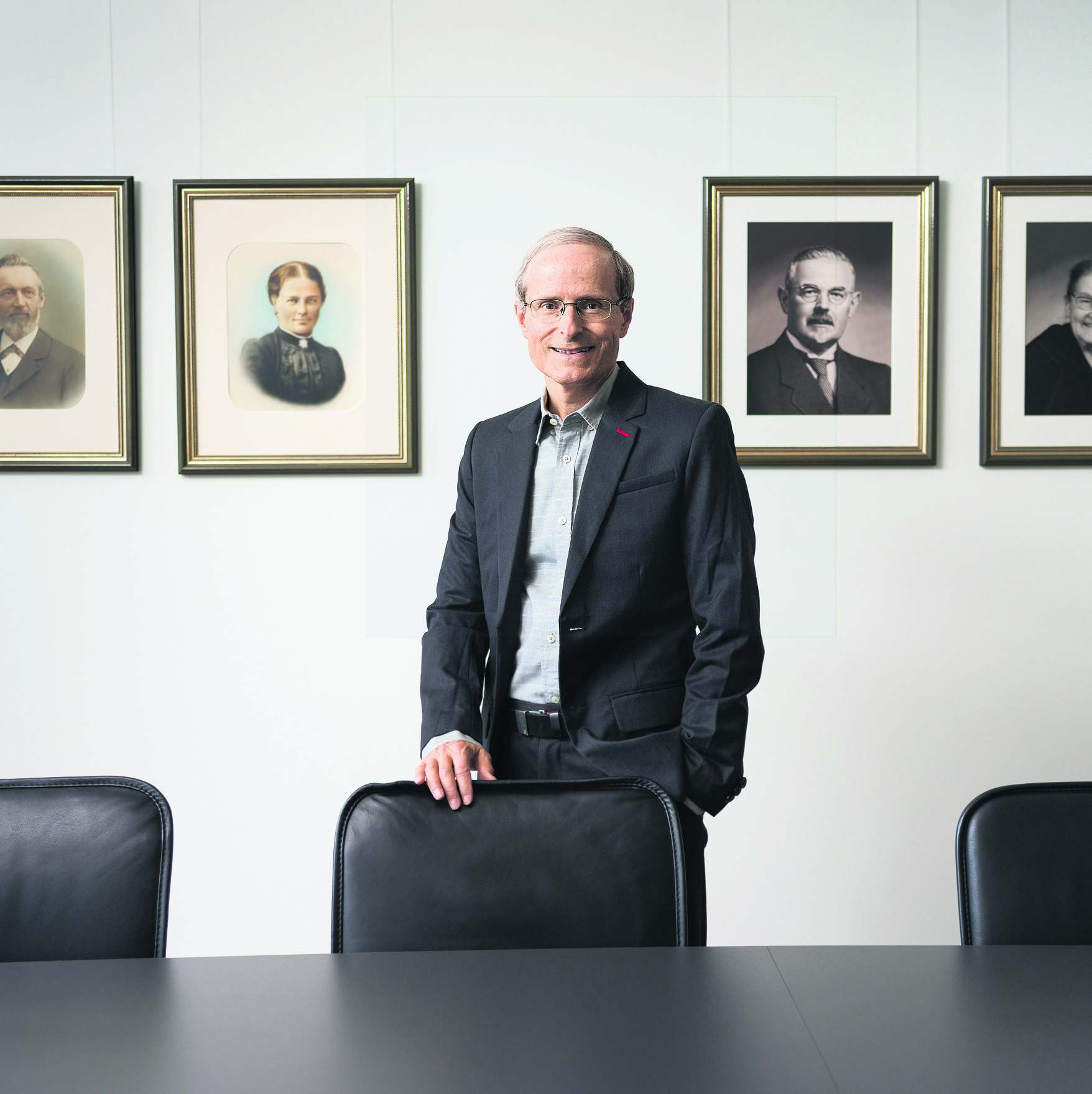
A la tête de l’entreprise familiale, le CEO Carl Elsener représente la quatrième génération de ce bijou de la coutellerie suisse qu’est Victorinox. Fondé en 1884, l’atelier (devenu une imposante manufacture) se situe toujours à Ibach, dans le canton de Schwytz. C’est de là que le légendaire couteau suisse part à la conquête de plus de 120 pays. L’activité s’est diversifiée dans la coutellerie ménagère et professionnelle, puis dans la bagagerie et les montres, plus récemment la parfumerie. En 2019, l’entreprise comptait 2100 employés et assurait un chiffre d’affaires de 480 millions.